Caterpillar Sealing O-ring Family Unveiled
Performance Unveiled: Why Are They the First Choice for Sealing?
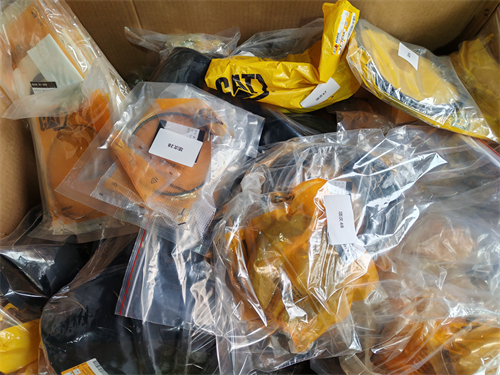
(1) The Mystery of Materials
Caterpillar's O-ring models are extremely meticulous in material selection, using materials that perfectly match the oil, temperature, and pressure in the engine and machine. Taking the common nitrile rubber (NBR) as an example, it has good resistance to mineral oil, lubricating oil, etc., and can maintain stable physical properties in the temperature range of -40 ℃ to 120 ℃. In the high-temperature and high-pressure working environment of Caterpillar engines, O-rings made of nitrile rubber are not easily corroded by oil and always maintain good elasticity and sealing performance. Moreover, these materials have excellent wear and extrusion resistance, and will not easily wear or deform under frequent relative motion and strong pressure of mechanical components, greatly extending their service life. At the same time, they also have excellent resistance to compression deformation, and can quickly recover to their original state even after being compressed for a long time,
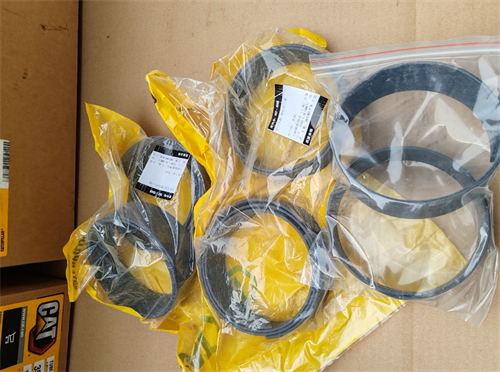
ensuring consistent sealing effect.
(2) Precision manufacturing process
Dimensional accuracy is crucial for the sealing performance of O-rings. Caterpillar's O-rings such as 7m-9909, 7m9909, 8n2410, and 8n-2410 strictly follow the tightness tolerance during the manufacturing process. This high-precision manufacturing process ensures that the O-ring can fit snugly into the sealing groove with just the right sealing compression. When the O-ring is installed in the sealing groove of a mechanical component, its precise size ensures a tight fit with the groove wall without any gaps, effectively preventing fluid leakage. If the size deviation is too large, the O-ring may not be able to fully fill the groove, resulting in seal failure. Caterpillar's precision manufacturing process avoids this situation and provides a solid guarantee for the stable operation of the machinery.
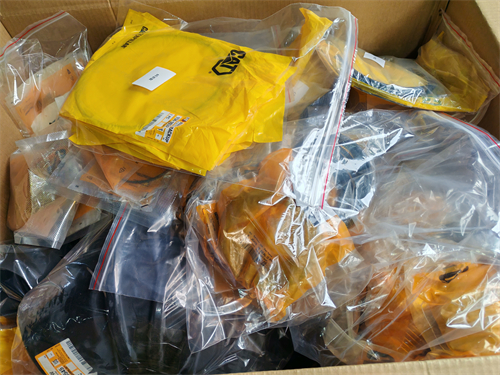
(3) The advantages of special coatings
Some Caterpillar O-rings are coated with polytetrafluoroethylene (PTFE) coating, which brings many advantages. During the installation of seals, PTFE coating can significantly reduce the twisting and cutting experienced by the seals. During the mechanical installation process, the O-ring may deform or be damaged due to friction or collision with the installation site. With PTFE coating, it is like putting a layer of "protective clothing" on the O-ring, reducing these risks. For example, in the installation of hydraulic system pipelines, O-rings coated with PTFE can be installed more smoothly, reducing sealing problems caused by improper installation and improving installation efficiency and sealing reliability.
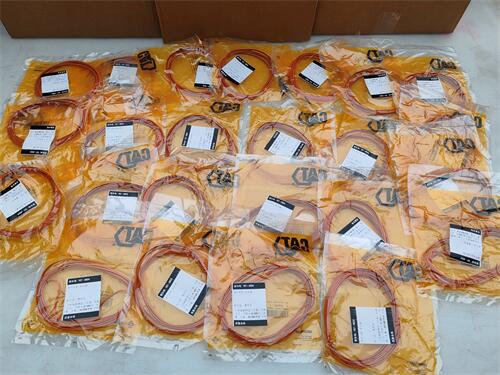
Application Scenario Grand Prize: Reliable Protection Everywhere
(1) Key role in the engine
In Caterpillar's engine field, O-rings play an irreplaceable role. Taking the Caterpillar 3512a diesel engine as an example, it is a commonly used power source for large construction machinery and power generation equipment, and its working environment is extremely harsh. Between the cylinder block and cylinder head of the engine, O-rings of models such as 7m-9909 and 8n-2410 form an indestructible sealing barrier. When the engine is running, high temperature and pressure are generated inside, and the oil and coolant circulate in complex pipelines. The O-ring effectively prevents the leakage of liquids such as oil and coolant. If there is a problem with the O-ring here, oil leakage can cause insufficient lubrication between the internal components of the engine, exacerbate wear, increase frictional resistance, reduce engine power, and even cause engine failure and shutdown in severe cases. Leakage of coolant can cause the engine to fail to dissipate heat properly, resulting in a sharp increase in temperature and potentially causing serious consequences such as cylinder deformation and piston jamming. Maintenance costs are high and can delay project progress.
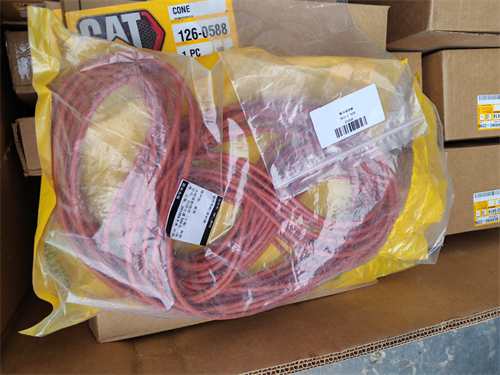
(2) Close partner of hydraulic system
In the hydraulic system of excavators, hydraulic oil is the key medium for transmitting power, and O-rings are the core components that ensure stable operation of the hydraulic system. The hydraulic system drives various working components through the pressure changes of hydraulic oil, such as the lifting and lowering of the boom, the extension and retraction of the boom, and the loading and unloading of the bucket, all of which rely on the precise control of the hydraulic system. O-rings such as 7m9909 and 8n-2410 are widely used in the connection and sealing parts of hydraulic pumps, hydraulic cylinders, hydraulic valves, and other components. They prevent hydraulic oil leakage and ensure that the hydraulic system can maintain stable pressure. Once the O-ring seal fails and hydraulic oil leaks, the system pressure will decrease, causing the excavator to operate slowly, weakly, or even fail to function properly. Moreover, hydraulic oil leakage not only causes resource waste, but may also pollute the working environment, increase equipment maintenance costs, and pose safety risks.
Installation and Maintenance: The Secret to Extending Service Life
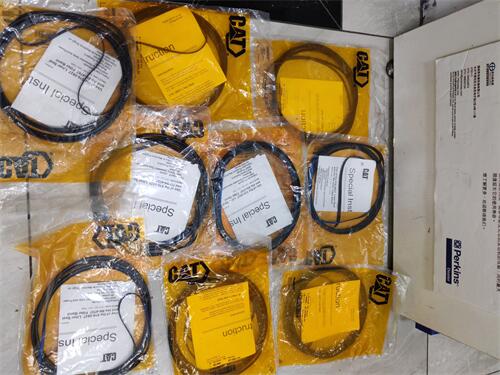
(1) Correct Installation Guide
Installing Caterpillar O-ring seals is a delicate task that requires careful operation. Before installation, it is necessary to strictly clean the sealing groove and sealing surface. Any small impurities, such as dust, metal debris, etc., may cause scratches and damage the sealing performance during the installation and operation of the O-ring. Professional cleaning agents and clean cloths can be used for wiping to ensure a clean and tidy surface. Meanwhile, during the assembly process of the O-ring, an appropriate amount of lubricating grease should be applied to the surface it passes through. Lubricating grease can not only reduce the friction between O-rings and other components during installation, but also prevent O-rings from being scratched or twisted, allowing them to be installed smoothly in place.
To avoid sharp edges such as sharp corners and threads from cutting the O-ring during installation, a 15 ° -30 ° introduction angle should be reserved at the shaft and hole ends of the installation to allow the O-ring to enter the installation position more smoothly. When the O-ring needs to pass through the external thread, a specialized thin-walled metal guide sleeve should be used to cover the external thread; If the O-ring needs to pass through the hole, the hole should be inverted into a corresponding oblique shape, and the bevel angle is usually 120 ° -140 ° to prevent the O-ring from being scratched. During the installation process, it is also necessary to ensure that the O-ring is fully embedded in the groove to avoid twisting or stretching, especially in narrow spaces, and to be careful when operating to prevent the O-ring from being clamped or damaged.
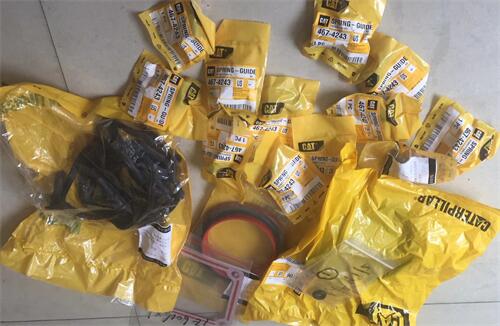
(2) Key points of daily maintenance
Regularly checking the wear and aging of O-rings is key to daily maintenance. It is generally recommended to establish a reasonable inspection cycle based on the frequency of device usage and working environment, such as conducting an inspection once a week or once a month. During inspection, carefully observe the surface of the O-ring for signs of cracks, wear, hardening, or deformation. If obvious cracks are found on the surface of the O-ring, it means that its structure has been damaged and its sealing performance will be greatly reduced; If the O-ring hardens, it may have aged and lost its original elasticity, making it unable to effectively seal; Severely worn O-rings can change in size and shape, leading to seal failure. Once these situations occur, the O-ring should be replaced promptly.
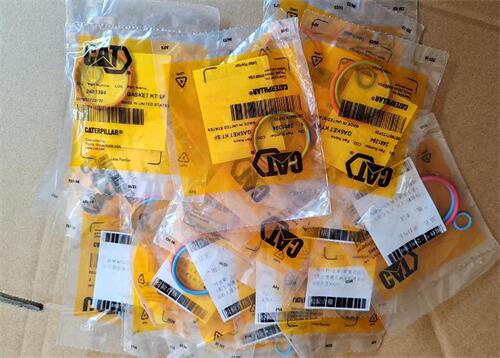
In addition, some simple methods can be used to assist in determining whether the O-ring needs to be replaced. For example, during the operation of the equipment, pay attention to whether there is any fluid leakage. If a small amount of oil, coolant, or gas leakage is found, it is likely that there is a problem with the sealing performance of the O-ring. At the same time, pay attention to the working status of the equipment. If there is abnormal vibration, noise, or performance degradation, it may also be related to damage to the O-ring. Timely replacement of problematic O-rings can not only ensure the normal operation of the equipment, but also avoid major losses due to minor issues, reduce maintenance costs and downtime caused by equipment failures.