(1)喷射延迟阶段
喷油器向气缸喷油的时刻比油泵内压力开始上升的时刻要落后一段时间。造成这种现象的主要原因,首先是由于出油阀上的卸荷容积作用,当油泵压力开始上升时,必须等到卸荷容积与高压油管相同后,燃油方能进入高压油管;其次,是在高压下因燃烧和高压油管的弹性作用,燃油被压缩而高压油管内的容积增大,故压力上升较缓慢。
所以在喷油泵供油开始后,高压系统中的油压升高,直到喷油器内压力升到针阀的启阀压力时,针阀才能开启上升,使燃油喷入汽缸。
(2)主要喷射阶段
喷油器内的压力较高,大部分燃油在此阶段喷入汽缸,而且是在不断增高的压力下喷入的,其雾化效果比较理想。次阶段取决于柴油机的负荷,负荷越大,此阶段越长。
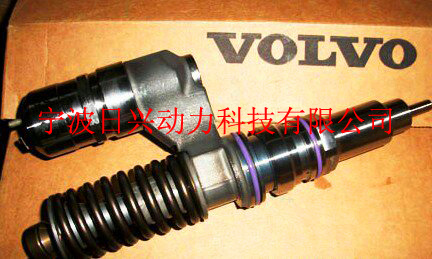
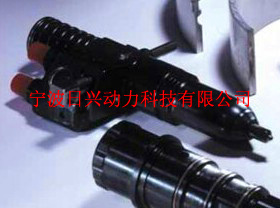
(3)滴漏阶段
在这阶段中,喷油器的压力从最高喷油压力一直下降到针阀的落座压力。
3、喷油规律及其要求
Fuel injection and combustion system for diesel generator engine
First, diesel engine fuel injection
1, the composition of the fuel injection system
Role of the fuel injection system, is at a very high pressure at a certain moment will quickly a certain number of fuel injected into the cylinder, make it spray. Injection system is composed of the main device is fuel injection pumps, injectors and high-pressure tubing.
2, injection process
Characteristics of injection process can be divided into Jet delayed, spray and drip three main stages.
(1) blast delayed phase
Fuel injector cylinder pressure began to rise within the moment of injection pump always lagged behind those for some time. Caused this phenomenon of main causes, first is due to out valve Shang of unloading Dutch volume role, dang pump pressure began rose Shi, must until unloading Dutch volume and high pressure tubing same Hou, fuel party can entered high pressure tubing; second, is in high pressure Xia due to combustion and high pressure tubing of elastic role, fuel was compression and high pressure tubing within of volume increases, so pressure rose more slow.
So after the start of injection pump oil, hydraulic high pressure system rises, until the needle valve of injector pressure rise when Kai valve, needle valve can be opened up, fuel injected into the cylinder.
(2) the main injection phase
Higher pressure in the injector, and most of the fuel injected into the cylinders at this stage, but is under pressure from the rising spray into, ideally its fog effects. Second phase depending on the load of diesel engine, large loads this phase longer.
(3) the dripping phase
In this phase, the injector pressure maximum injection pressure has been down to needle valve seat pressure.
3, injection and its requirements
(1) fuel injection rate
The so-called injection, is a cyclic injection quantity distribution throughout the injection duration, that is, each ' participation in distribution curve of the handle angle spray oil.
(2) injection delays
Fuel injection delay was mainly due to fuel can be compressed, high pressure oil pipe caused by fluctuation phenomena in elastic and high pressure tubing.
4, the factors affecting fuel injection rate
(1) cam curve and effective work
Fuel pump cam determines the plunger motion law, and rapid variation of the plunger pump decision for law, thus affecting the injection. Effectively in the piston stroke and starting point for oil under the same circumstances, cam shape more steep, oil rise faster, larger oil supply speed, fuel injection delays and injection angles the smaller.
(2) the piston diameter and orifice diameter
Without changing the piston stroke increases when the piston diameter, speed increases for oil, fuel injection delays and continuous angles are reduced, in favour of combustion in the previous check point near the end, diesel economy getting better. But the initial injection rate to increase, will participate in the burning oil increased when the fire started, running rough.
When the injector fuel injection hole diameter hole does not change the number of hours, due to the resistance increase of sprayed oil injection angle increases, and each cam rotating angle of injection quantity decreases. At this point, due to the increasing pressures of high pressure tubing and are prone to repeated injection.
(3) high pressure oil pipe size
Long high pressure tubing, oil spraying large delay angle and Jet Yau continued basically unchanged. That is as high pressure tubing length increases, its actual fuel injection advance angle is smaller. If does not equal the length of each cylinder of high pressure tubing, you will make each cylinder injection vary, this is the effect of multi-cylinder diesel engine is not working even one reason. In order to make consistent cylinder injection, each cylinder of high pressure tubing length the same as much as possible.
Smaller tubing inner diameter, greater fuel flow resistance, oil spraying large delay angle.
(4) diesel engine load and speed
When the speed of diesel engine and fuel injection timing does not change, if the increased load, its fuel injection fuel injection end change starting point is essentially the same, and increased during the second half of the injection quantity.
When the load of diesel engine and fuel injection timing does not change when you change the speed, as the speed increases, the corresponding time shortening of each cam rotating angle, so fuel injection delays and injection angles are increasing, and each cam rotating angle of injection quantity reduction.
1, exception, Jet
(1) repeat injection (secondary injection)
When the end of the injection pump and oil, again after the injector needle valve seat was lifted by hydraulic spray phenomenon known as repeat injection, also known as secondary injection. This phenomenon in diesel engines under high speed loading condition most likely to occur. Disadvantages of repeated injection is on the one hand will make the injection angle larger, on the one hand because of late under low pressure fuel injection, resulting in deterioration of the reduced quality of atomization, combustion and smoke rise, parts overheating, such as bonded carbon in combustion chamber and exhaust black smoke, thereby reducing the reliability and economy of the diesel engine.
(2) intermittent injection
During the oil supply in fuel injection pump, injector needle valve intermittent opening and closing (frequent ups and downs), inadequate and insufficient lift, Jet, a phenomenon known as intermittent spraying. Its easy to occur under conditions of low speed.
(3) unstable Jet and alternate Jet
Unstable injection refers to the injection pump can continue working, but the oil circulating spray in spray changing circumstances. Their extreme lapse of time Jet, spray only twice in every oil fuel injector for fuel injection pump oil. This situation is occurring in diesel engines at low speed under low load conditions. When there were intervals when, a loop is not firing, so the gallop.
Second, diesel engine fuel injection pump and injectors
Requirements for fuel injection device
(1) fuel atomization
Good atomization of fuel, is the foundation of good combustion process, mainly by providing some fuel injection pressure of injection pump and injectors sprayed, and to guarantee. Higher fuel injection pressure, fog effects are better.
(2) to correct injection timing
To ensure the realization of good combustion process, to correct injection timing is also an important factor. For efficient combustion process, generally before the TDC will fuel injected into the cylinder. Fuel injected into the cylinders crank angle between the point and the ending point on, known as the "fuel injection advance angle", and pumps on the start point for oil and crank angle between the points. Known as the "fuel supply advance angle". Fuel injection device must to correct injection advance angle of fuel injected into the cylinder.
Fuel injection fuel supply advance angle of advance angle mainly by decision, and fuel supply advance angle is determined by the fuel injection pump cam to the installation location. Calibration conditions fuel supply advance angle of experimental determination by the factory. But Dang using of fuel quality change Shi, fuel of delay burning period occurs changes, above by requirements of for oil ahead of corner to again adjustment; also, more cylinder diesel engine due to spray pump and cam manufacturing Shang of difference and using in the of wear different, despite the spray pump cam of installed angle same, but the cylinder of actual for oil ahead of corner still has difference, so requirements the cylinder of spray oil timing can separate regulation. Adjust injection timing is mostly achieved through changing the installation position of cams on the camshaft.
(3) fuel delivery adjustments
Each cycle of the diesel engine in the amount of fuel injected into the cylinder size determines the power of diesel engine, in order to adapt to changes in engine load, fuel injection pumps should be able to adjust according to the load injection quantity, this kind of adjustment is known as "general tone". Multi-cylinder diesel engine, each cylinder injection quantity should be equal, or high load, some cylinders may overload due to fuel injection too much; and at low load, some less cylinder injection quantity might stop working. In theory, each cylinder fuel injection pump for oil should be the same, but due to differences in manufacturing and use of injection pump wear in different, and when installed improperly adjusted and other reasons, virtually impossible to uniform. Therefore, in addition to requests by the General call, also can be adjusted independently.
(4) other requirements
From the perspective of maintaining stable performance of diesel engines, ask the fuel injection device will succeed in making repeated injection, intermittent Jet injection, instability and isolation exceptions such as Jet spray.
From a trading perspective, requirements of fuel injection equipment reliable, convenient adjustment, can quickly stop oil.
Third, the diesel engine mixture formation and combustion
1, the main factors affecting fuel atomization
(1) fuel injection pressure
When the fuel injection pressure increases, improve atomization fineness and uniformity, fuel spray cone angle and range increased, improved quality of atomization.
(2) number of orifice hole
Nozzle total circulation area in the same case, the more many nozzle holes, its smaller diameter, atomization fineness and uniformity increase fuel spray cone angle increased, but declining range. Number and diameter of orifice hole is determined by the fuel spray and combustion chamber for the best match to.
(3) spray the hole diameter
When the orifice diameter increases, atomizing fineness and evenness are declining, but increases the range of fuel spray cone angle decreases. Instead, when the orifice diameter decreases, atomizing improve fineness and uniformity, reduce the range of fuel spray cone angle increases.
(4) fuel viscosity
When the oil viscosity increases, due to its poor mobility, divided more difficult, atomization from malnutrition.
(5) the Jet back pressure
When the Jet back pressure increases, the density of compressed air in the cylinder increases, when fuel injection was the resistance increases, improved quality of atomization, cone angle is larger, but shorten the range.
2, on the combustion process of diesel engine requirements
General requirements for diesel engine combustion process are: combustion totally smooth, speedy and timely, not gross, air a high utilization rate.
Four, diesel engine fault inspection
1, fuel pump main failure
Injection pump plunger sleeve are the main parts, valve and valve seat two precision coupling, so most of the major faults of injection pump occurs in two parts.
(1) the cavitation
In the fuel injection system, when a fuel pressure drops below or equal to the temperature of vaporization of fuel pressure, started the fuel gasification and bubble, followed by rupture of bubbles under positive pressure wave, and inspire very strong impact, effect on the metal surface. This repeated erosion, cavitation damage will cause a metal surface, making fuel injection system parts damaged. System locations most susceptible to cavitation in fuel injection pump valve and valve seat seal, pump body corresponding to the oil return holes, inner wall of high pressure oil pipe and injector needle valve seal.
Cavitation high pressure system can be resolved by selecting Uninstall volume of delivery valve, low-voltage system of cavitation, accessible through the increasing pressures of fuel oil or oil recovery setting in the system buffer solutions.
(2) excessive wear and tear, napping, piston and sleeve garter and bitten to death
Excessive wear of the piston and sleeve will degrade sealing, resulting in poor atomization of fuel injection pressure is reduced, non-uniform, the amount of each cylinder's injection and combustion issues of deterioration.
Piston clamping and bitten to death would cause the cylinder oil pump is not available for stopping work. Caused reason for clamping or bitten to death, mostly fuel cleaning bad quality, impurity particles in oil. In the particular case, or may be installed incorrectly or too small a gap, or excessive working temperatures, temperature changes caused by too fast.
(3) wear of valve and valve seat, valve stem stuck or killed
After the valve and valve seat wear, seal decline, caused decline in the residual pressure or high pressure pipeline injection quantity decrease, affecting the quality of atomization and combustion processes. Valve and valve seat wear caused by reasons, mainly oil impurities in fuel, acid corrosion, impact or valve distortion, and so on.
Stem clamping or bitten to death may be due to poor lubrication, unevenly, could also be valve rods and bushings resulting from deformation. Corresponding failures occurred because the valve does not properly. For example: stem valve open position stuck, then the return valve cannot be closed, making stops for fuel injection pump for oil.
2, checking and adjustment of fuel injection pump
Function of the injection pump is scheduled to fuel injector with a certain pressure, quantitative, so it should also be focused on sealing, check and adjust the timing and amount of oil for these three aspects.
(1) fuel pump seal check
Main check piston injection pump sealing sleeve parts, valve and inlet and outlet valves.
① comprehensive inspection
Fitted with pressure gauge at the exhaust tubing connector, shake the lever with your hand pump, when the oil reaches manual stop when under pressure
Pump oil, keep the piston position, watch the pressure gauge pressure. If the time specified in the instructions (usually a 30s) pressure remains unchanged, fuel injection pump sealing is considered good, otherwise, seal the bad.
When injection pump seals are found when bad, should be based on the construction of injection pump, outlet valve and inlet and back separately check valve and piston parts.
② outlet valve check
Outlet valve seal check procedures and comprehensive inspection of the same, but when under pressure in the hydraulic achieve statement,
Let the plunger naturally downward in order to specifically check out valve seal.
③ remove the outlet valve check
Valve is removed, check the comprehensive inspection procedure, mainly check the piston and intake, return valve seal
Sexual.
When totally worn out parts are found, should be renewed. Coupling grinding recovery.
(2) checking and adjustment of oil supply timing
Under optimal fuel supply advance angle of calibration experiment to determine and indicate the diesel engine by the factory manual, oil supply cam installed in order to ensure that most perspective prevails. However, when use of the fuel quality changes, fuel supply advance angle should be readjusted; in addition, each cylinder firing when not in uniform, to adjust the cylinder alone advance angle.
① oil supply timing of checks
Oil a, risking method
Bleed method in check when the injection timing should be removed on the injection pump high pressure oil pipe. Put on dedicated check oil
Tube. The throttle to the calibration oil supply position, several oil pump, tubing run after oil, will erase the flowlines surface. Then press the cars slowly turning, while complying with the outlet surface. When the liquid level began to rise this time scale the cylinder on the flywheel fuel supply advance angle.
This law only applies to small and medium diesel engines, larger piston diameter of diesel engine, fuel injection time shorter, due to this law room for larger errors, inappropriate use.
B, illumination method
Regulation of big oil return hole end type fuel injection pump, if the sleeve on the same high, oil return holes available illumination method for measuring time. Disassemble the pump body corresponding to the oil return holes on the screw slowly turning, with torch lighting from the oil hole. When the column just north of the Great Wall line oil hole covers back to see when the light, to stop turning, this time on the flywheel pointer indicates the scale of the oil pump and oil starting point, that is, fuel supply advance angle.
C, mark law
Some starting points for oil pump of diesel engine injection pump body equipped with fixed and sliding tag. When turning, from gap (Windows) see tags moment of coincidence, is the starting point of injection pump for oil.
② oil supply timing adjustment
Adjustment of oil supply timing achieved mainly through two channels: one way is to change the relative position of the cam and camshaft, changing the relationship between cam and crankshaft timing, so as to achieve change timing adjustment of oil supply; another way is to change the chute and plunger sleeve relative location oil return holes, change cam to work effectively to achieve oil supply timing adjustments. To change the relative positions of the chute and plunger sleeve, there are two ways to achieve: move the plunger up and down and up and down the sleeve. Adjustment of oil supply timing by rotating cams law
(1)喷油规律
所谓喷油规律,是一个循环的喷油量在整个喷射延续时间内的分配情况,即每度曲柄转角喷出油量的分配曲线。
(2)喷油延迟
喷油延迟主要是由于燃油的可压缩性、高压油管的弹性以及高压油管中的波动现象造成的。
4、影响喷油规律的因素
(1)凸轮曲线和有效工作段
油泵凸轮型线决定了柱塞运动规律,而柱塞的迅速变化规律决定油泵的供油规律,从而影响喷油规律。在柱塞有效行程和供油始点相同的情况下,凸轮外形越陡,油压上升越快,供油速度越大,喷油延迟角和喷油持续角就越小。
(2)柱塞直径和喷孔直径
在不改变柱塞行程而增大柱塞直径时,供油速度增大,喷油延迟角和持续角均减小,有利于燃烧在上止点附近结束,柴油机经济性变好。但初期的喷油速率提高,会使燃烧开始时参加燃烧的油量增多,运转粗暴。
当喷油器的孔数不变而喷油孔直径变小时,由于喷油阻力的增加使喷油持续角增大,而每度凸轮转角的喷油量减小。此时,由于高压油管中的压力增高,容易产生重复喷射。
(3)高压油管尺寸
高压油管越长,喷油延迟角越大而喷油持续角基本不变。也就是说随着高压油管长度的增加,其实际喷油提前角却变小了。如果各缸高压油管的长度不相等,则将使各缸喷油规律有所差别,这也是影响多缸柴油机工作不均匀的原因之一。为了使各缸喷油规律一致,应尽可能使各缸的高压油管长度相同。
油管内径越小,燃油流动阻力越大,喷油延迟角越大。
(4)柴油机负荷与转速
当柴油机转速及喷油定时不变时,若增大负荷,其喷油始点基本不变而喷油终点改变,并且增加了后半期的喷油量。
当柴油机负荷及喷油定时不变而改变转速时,随着转速的增加,相应每度凸轮转角的时间缩短,故喷油延迟角和喷油持续角均增大,而每度凸轮转角的喷油量减少。
1、 异常喷射
(1)重复喷射(二次喷射)
当喷油泵供油结束,喷油器针阀落座后有重新被油压抬起的喷射现象称为重复喷射,又叫二次喷射。这种现象在柴油机高转速大负荷的工况下最容易发生。重复喷射的缺点是一方面会使喷油持续角变大,另一方面由于后期在低压下喷油、致使雾化质量降低、燃烧恶化、排烟升高、机件过热、燃烧室结碳、排气冒黑烟等,从而降低了柴油机的可靠性和经济性。
(2)断续喷射
在喷油泵的一次供油期间,喷油器针阀断续启闭(频繁地起落),而且起升不足、喷射不力,这种现象称为断续喷射。其容易在低转速的工况下发生。
(3)不稳定喷射和隔次喷射
不稳定喷射是指喷油泵虽能持续工作,但各循环喷油量在喷射时不断变动的情况。其极端的情况时隔次喷射,即喷油泵每供油两次喷油器才喷一次油。这种情况也是在柴油机低速低负荷的工况下发生的。当发生隔次喷射时,一个循环不发火,故运转不稳定。
二、柴油发动机喷油泵及喷油器
对喷油设备的要求
(1)燃油的雾化
燃油的良好雾化,是实现良好燃烧过程的基础,主要靠喷油泵提供的一定喷油压力和喷油器喷和来保证。喷油压力越高,雾化效果越好。
(2)正确地喷油定时
要保证实现良好的燃烧过程,正确地喷油定时也是一个重要的因素。为实现高效的燃烧过程,一般均在上止点前就将燃油喷入气缸。燃油喷入气缸点与上止点之间的曲柄转角,称为“喷油提前角”,而油泵开始供油点与上止点之间的曲柄转角。称为“供油提前角”。喷油设备必须以正确的喷油提前角将燃油喷入气缸。
喷油提前角主要由供油提前角决定,而供油提前角则由喷油泵凸轮的安装位置来决定。在标定工况下的供油提前角由工厂试验确定。但是当使用的燃油品质变更时,燃油的滞燃期发生变化,上述所要求的供油提前角要重新调整;另外,多缸柴油机由于喷油泵和凸轮制造上的差别和使用中的磨损不同,尽管各喷油泵凸轮的安装角度相同,但各缸的实际供油提前角仍有差别,故要求各缸的喷油定时能单独调节。调节喷油定时大多是通过改变凸轮在凸轮轴上的安装位置来实现的。
(3)供油量的调节
在柴油机每循环中喷入汽缸的燃油量决定着柴油机的功率大小,为适应柴油机负荷的变化,喷油泵应能根据负荷来调节喷油量,此种调节称为“总调”。在多缸柴油机中,各缸喷油量应该均等,否则在高负荷时,某些气缸可能因喷油量过多而超负荷;而在低负荷时,某些气缸可能因喷油量少而停止工作。理论上,各缸喷油泵的供油量应该是一样的,但由于喷油泵制造上的差别和使用中磨损的不同,以及安装时调节不当等原因,实际上不可能均匀。因此,除了要求由总调外,还应可以进行单独调节。
(4)其它要求
从保持柴油机性能稳定的角度出发,要求喷油设备能根绝重复喷射、断续喷射、不稳定喷射和隔次喷射等异常喷射现象。
从营运角度出发,要求喷油设备工作可靠、调节方便、能迅速停油。
三、柴油发动机混合气的形成和燃烧
1、影响燃油的雾化的主要因素
(1)喷油压力
当喷油压力增大时,雾化细度及均匀度提高,油束锥角和射程增大,雾化质量提高。
(2)喷孔孔数
在喷油嘴总流通面积不变的情况下,喷孔孔数越多,其直径越小,雾化细度和均匀性提高,油束锥角增大,但射程下降。故喷孔孔数和直径是是由油束与燃烧室获得最佳匹配来决定的。
(3)喷孔直径
当喷孔直径增大时,雾化细度和均匀度均下降,但油束射程增大而锥角减小。相反,当喷孔直径减小时,雾化细度及均匀度提高,油束锥角增大而射程减小。
(4)燃油粘度
当燃油粘度增加时,由于其流动性差,分裂较困难,故雾化不良。
(5)喷射背压
当喷射背压增加时,即缸内压缩空气的密度增加,燃油喷射时受到的阻力增加,因此雾化质量提高,锥角变大,但射程缩短。
2、柴油机对燃烧过程的要求
对柴油机燃烧过程的总要求是:燃烧完全、迅速及时、工作平稳不粗暴、空气利用率高。
四、柴油发动机故障检验
1、喷油泵的主要故障
喷油泵的主要零件是柱塞套筒、阀及阀座两对精密偶件,因此喷油泵的主要故障大多发生在这两对零件上。
(1)穴蚀
在燃油喷射系统中,当某处的燃油压力下降到低于或等于该温度下的燃油汽化压力时,该处燃油就开始气化而产生气泡,随后气泡在正压力波的作用下破裂,并激发出很强的冲击力,作用在金属壁面上。这样反复地侵蚀,就会引起金属表面穴蚀破坏,使喷油系统零件损坏。系统中最易发生穴蚀的地点有喷油泵阀与阀座的密封处、与回油孔相对应的泵体、高压油管内壁及喷油器针阀密封处。
高压系统中的穴蚀可通过选择出油阀的卸载容积来解决,低压系统中的穴蚀,可通过提高进油腔的燃油压力或在回油系统中设置缓冲器的方法来解决。
(2)柱塞和套筒过度磨损、拉毛、卡紧和咬死
柱塞和套筒的过度磨损会使密封性下降,造成喷油压力降低、雾化不良、各缸喷油量不均匀和燃烧恶化等问题。
柱塞卡紧和咬死会引起油泵不能供油而使气缸停止工作。造成卡紧或咬死的原因,大多是燃油净化质量不良,油中应有杂质颗粒。在个别情况下,也可能是安装不正确或间隙过小,或工作温度过高,温度变化过快所致。
(3)阀和阀座磨损、阀杆卡死或咬死
阀和阀座磨损后,密封性下降,使高压油管中的剩余压力下降或造成喷油量减小,影响雾化质量及燃烧过程。造成阀和阀座磨损的原因,主要是油中有杂质、燃油的酸性腐蚀、撞击或阀面扭曲变形等。
阀杆卡紧或咬死的原因可能是润滑不良、受热不均,也可能是阀杆及导套变形而引起。这时将会因阀不能正确动作而发生相应的故障。例如:阀杆在阀开启位置卡死,则回油阀不能关闭,使喷油泵停止供油。
2、喷油泵的检查与调整
喷油泵的功能是定时、定量地向喷油器提供一定压力的燃油,所以对它的检查和调整也应着重在密封性、定时及供油量这三个方面。
(1)喷油泵密封性检查
喷油泵密封性主要检查柱塞套筒偶件、出油阀偶件及进、出油阀。
① 综合检查
在排油管接头处装上压力表,用手摇动杠杆油泵,当油压达到说明书规定的压力时停
止泵油,保持柱塞位置,观看压力表的压力。如果在说明书规定的时间(一般为30s)内压力保持不变,则认为喷油泵密封良好,否则密封不良。
当发现喷油泵密封不良时,应根据喷油泵的构造,分别对出油阀和进、回油阀以及柱塞偶件进行检查。
② 出油阀检查
出油阀的密封性检查的步骤与综合检查相同,只是在油压达到说明书规定的压力时,
让柱塞自然下行,以便专门检查出油阀的密封性。
③ 取出出油阀检查
取出出油阀后,按综合检查的步骤进行检查,主要检查柱塞偶件及进、回油阀的密封
性。
当发现磨损过度的零件时,应予换新。偶件应研磨恢复。
(2)供油定时的检查与调整
标定工况下的最佳供油提前角由工厂试验确定并注明在柴油机的说明书上,供油凸轮的安装以保证这个最挤角度为准。但是,当使用的燃油品质变更时,供油提前角应重新调节;另外,各缸发火不均匀时,要单独调整各缸提前角。
① 供油定时的检查
A、冒油法
在采用冒油法检查喷油定时的时候,应拆去喷油泵上的高压油管。换上专用的检查油
管。将油门置于标定供油位置,先使油泵供几次油,待油管冒油后,将出油管液面抹平。然后按正车方向慢慢盘车,同时注意出油口液面。当液面开始上升这一时刻飞轮上的刻度即为该缸的供油提前角。
此法只适用于中小型柴油机,对于柱塞直径较大、喷油时间较短的柴油机,由于此法容易出现较大的误差而不宜采用。
B、照光法
对大型回油孔终点调节式喷油泵,若套筒上有同样高的进、回油孔,可用照光法测量定时。拆下泵体上与进回油孔相对应的螺钉,缓缓盘车,从油孔处用手电筒照明。当柱塞上行刚好将回油孔遮住而看不到光线时,马上停止盘车,此时飞轮上指针所指示的刻度即为该油泵的供油始点,亦即供油提前角。
C、标记法
有些柴油机喷油泵的供油始点在泵体上装有固定和滑动标记。盘车时,当从缺口(窗口)处看标记重合的瞬间,即为喷油泵的供油始点。
② 供油定时的调节
供油定时的调节主要通过两条途径来实现:一条途径是改变凸轮与凸轮轴的相对位置,改变凸轮与曲轴的定时关系,从而达到改变定时供油的调节;另一条途径是改变柱塞斜槽与套筒回油孔的相对位置,改变凸轮的有效工作段来实现供油定时调整。而要改变柱塞斜槽与套筒的相对位置,又有两种方法可以达到:上下移动柱塞和上下移动套筒。故供油定时的调节有转动凸轮法、升降柱塞法及升降套筒法等三种。
A、转动凸轮法
凸轮轴是由曲轴带动的,两者之间存在着一定的定时关系,当凸轮与凸轮轴固定时,凸轮与曲轴之间亦有定时关系。而当改变凸轮与凸轮轴的相对位置时,凸轮与曲轴的定时关系也就改变了。转动凸轮法就是以此为基础进行供油定时调整的。
大中型柴油机中凸轮在凸轮轴上的固定方法,一般采用锥面齿定位、锁紧螺母压紧的方法实现。当调整凸轮与凸轮轴相对位置时,只要松开锁紧螺母,按需要转动凸轮后再上紧锁紧螺母即可。顺着凸轮轴旋转方向转动凸轮,则供油提前角增大,反之则减小。
B、升降柱塞法
升降柱塞法多用于中小型柴油机回油孔调节式喷油泵。升降柱塞,使得柱塞斜槽封闭回油孔的时刻发生变化,从而实现喷油定时的调整。
C、升降套筒法
升降套筒法与升降柱塞法类似,可用于回油孔调节式喷油泵。
3、喷油器的主要故障
(1)针阀偶件的磨损、漏油和卡紧
(2)喷孔磨损、结碳、阻塞和裂纹